The best time to insert an implant is immediately after a tooth has been extracted. The reason is that with time, the affected areas fall victim to atrophy, that is, a gradual loss of bone tissue. In case of severe bone atrophy, it becomes nearly impossible to install a dental implant without having to regrow tissue required for the procedure. Since tissue regeneration requires as long as six months, the dental sector has been actively adopting novel technologies to speed up the process. One of such advances is a personalized titanium membrane developed by ZERTAN in 2020.
“To receive a customized membrane, patients need to do a CT scan, which medical specialists need to create a computer model of their jaw. However, they can’t make it 3D until they have eliminated all the background noise and defects created by items such as tooth fillings, dental crowns, and other metal products. Today, this is done by dental technicians who need up to several hours to remove noise from the images. With this in mind, our company together with ITMO University tried to create a versatile and affordable tool that will perform these tasks in less time and more effectively,” says Ekaterina Zernitskaya, a dental surgeon and a co-founder of ZERTAN.
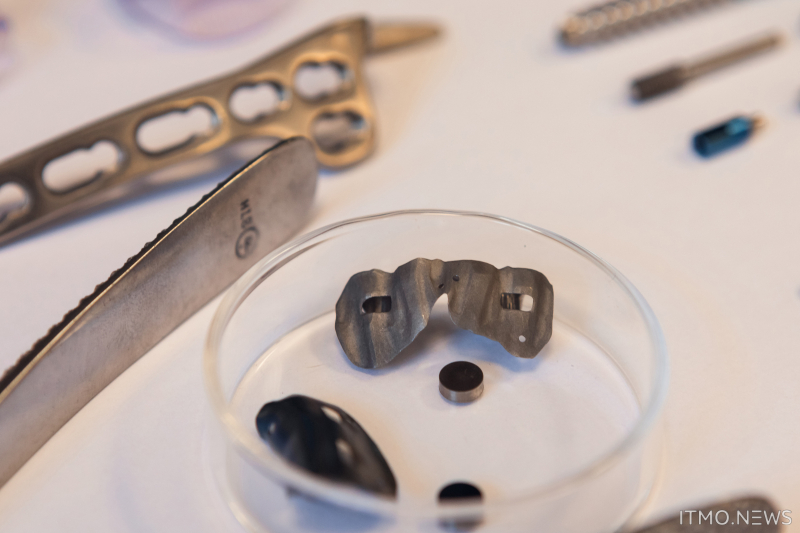
A personalized titanium membrane developed by ZERTAN. Photo by Dmitry Grigoryev / ITMO.NEWS
The researchers are currently working on an AI-based software that will allow technicians to model a membrane within several minutes. The developed neural network has already proven efficient in analyzing CT scans and producing a noise-free model of the skull. What takes a specialist at least two hours to complete, the program does in just a minute – more or less. The developers will continue to train the network using real-world data in order to increase its speed and accuracy.
“With this technology, we will be able to eliminate time-consuming, manual work from dental procedure. Our end product will, perhaps, be a website where specialists can process a certain number of scans within a subscription. This is how it will work: clinicians will load their CT scans into the system and within minutes, the program will offer them a 3D model of a membrane ready to go into production. Our colleagues are already testing the new software using their own cases to help develop its algorithms,” explains Galina Odintsova, a senior research associate at ITMO's International Research Laboratory for Micro- and Nanotechnology Lasers.
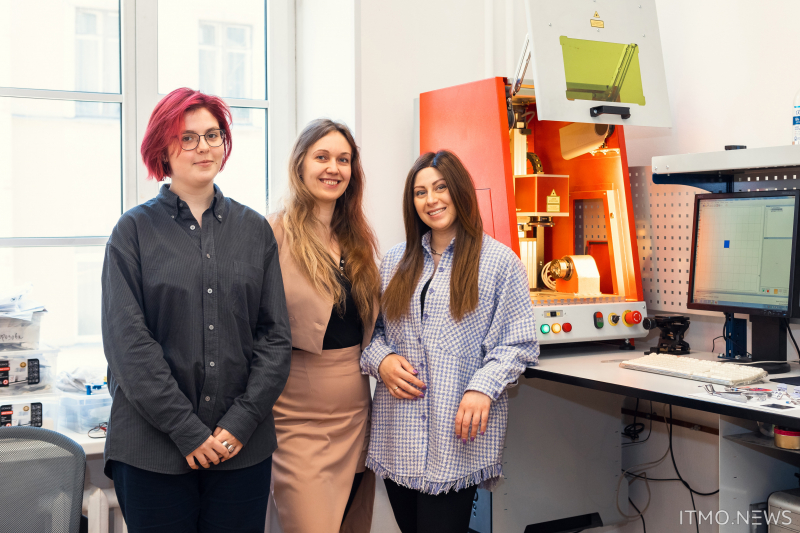
The research team (from left to right): Anastasiia Zavyalova, a first-year Bachelor’s student at ITMO’s Faculty of Nanoelectronics, Galina Odintsova, and Ekaterina Zernitskaya. Photo by Dmitry Grigoryev / ITMO.NEWS
Earlier on, researchers from ITMO also presented a method of improving the biocompatibility of implants through laser processing. Sales of the product began this year. Among the team’s other current projects are novel laser technologies and equipment that improve the antibacterial and hemostatic properties of various metal products used in medicine. The project received financial support under the Decree of the Russian Government No. 218.