Developing the implant
There are two factors that affect an implant’s integration into bone tissue: the surgery (the surgeon’s experience, sterilization of tools and instruments, and subsequent medical support) and the physical aspect (the size, shape, and surface of the implant). Laser processing of titanium makes it possible to contactlessly change the surface of the implant at the micro- and nano-scale. The technology eliminates the use of acids or abrasive particles, which otherwise remain on the surface and cause implants to have shorter lifespans of under 10-15 years.
The research project helped the scientists identify which surface structures – pits, elongated grooves, or disordered structures – ensure better compatibility between bone tissue and inorganic materials. Having tested several options, ITMO’s experts detected the best one: an elongated structure with microgrooves comparable to cells in size. This structure makes it possible to control the direction of tissue growth.
Applications in production
Researchers from ITMO University together with Lenmiriot, an ORTOS group company and the largest Russian full-cycle dental milling center, and the First Pavlov State Medical University of St. Petersburg used the new technology to produce dental implants. According to the developers, there are few cases of this method's commercial application in Russia and abroad.
“Every one of us has a different bone structure and that’s why each individual case requires its own type of implant. Lenmiriot produces over 100 types of them in different sizes, shapes, and conicity. We’ve developed processing techniques for all these types,” says Yulia Karlagina, an executor of the project and a researcher at ITMO’s International Research Laboratory for Micro- and Nanotechnology Lasers.
The production of each implant at the Lenmiriot facility consists of several steps. First, a titanium rod is transformed into the future implant of the needed size using micromilling and a 3D model. Then, the implant goes through several stages of cleaning, as well as laser processing that takes 20-40 minutes depending on the shape and form of the implant.
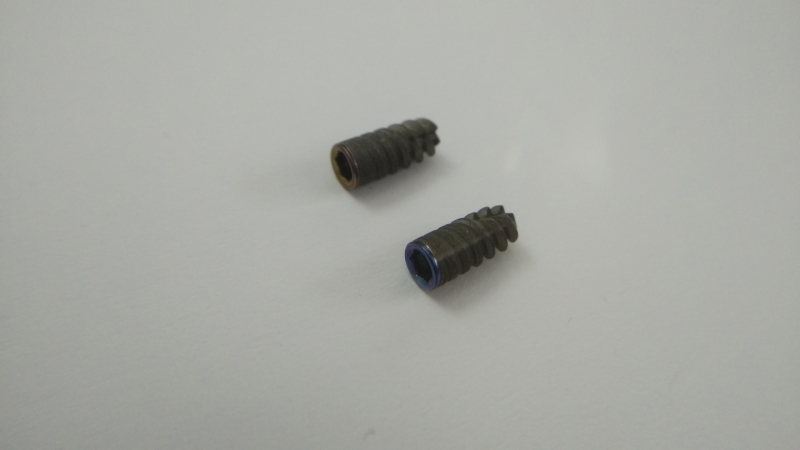
Laboratory prototypes of implants with different coatings. Photo courtesy of the International Research Laboratory for Micro- and Nanotechnology Lasers
Prospects of the technology
For their next project, the researchers are planning to develop the perfect implant with three functional zones. The first one is a root with microgrooves in its surface that will ensure integration with bone tissue. The second is the implant’s neck with a biomimetic surface and an antibacterial coating that will secure the device and prevent the formation of a bacterial biofilm. The third zone is the abutment, an element that connects the crown to the implant. In this case, the abutment has a smooth surface of different colors (i.e., blue, yellow, etc.) produced with laser processing. This element has antibacterial properties and serves as a dental indicator.
“We are also working on processing methods for other types of implants and enriching them with various functional properties. Moreover, we are currently developing a fully automated AI- and neural network-based technology for the development of personalized antibacterial titanium membranes,” adds Yulia Karlagina.