Lithography is a multi-stage process. Producing a small element requires expensive equipment and a team of specialists, which makes it exclusively available to large-scale companies that have the production of printed circuit boards streamlined. Others have to turn to specialized organizations and typically wait for over a month to receive their order; nevertheless, this does not rule out the possibility of a production error and the necessity to redo the order.
With this in mind, the scientists at ITMO University found a way to simplify and accelerate the process. They came up with a template-free laser metallization method that allows specialists to apply images even on curved surfaces. The method requires only a laser installation and a special chemical solution – and can be performed by a single specialist.
“In this case, the procedure is completed in three stages. First, the surface must be coated with a deep eutectic solvent. When two solid substances in such a solution are mixed, they lower one another’s melting points and form a viscous liquid that can easily dissolve metal salts. The plate is then put into a laser installation, which creates a pattern following a pre-set program. The laser beam heats the solvent film, causing a reduction reaction: a metal converts from an ionic to a metallic form. Afterward, the solution that is no longer needed is simply washed off,” explains Lev Logunov, PhD in chemistry, an author of the paper and a researcher at ITMO’s Faculty of Physics.
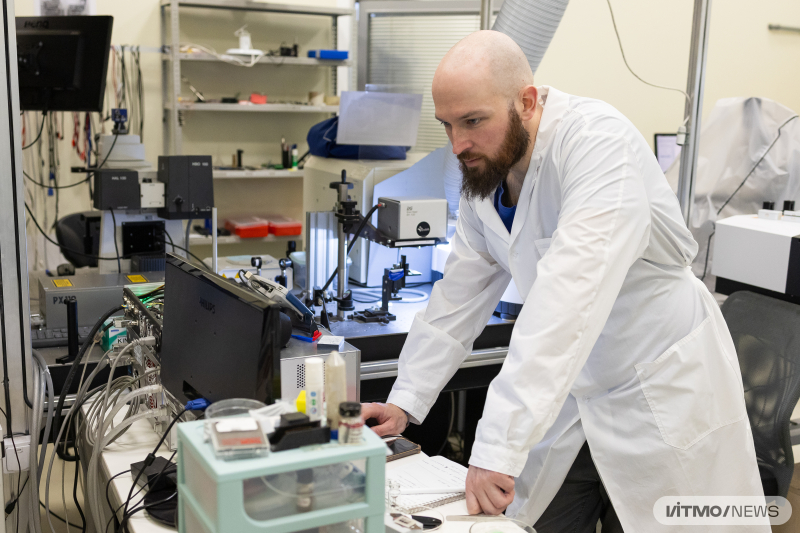
Lev Logunov at the laboratory. Photo by Dmitry Grigoryev / ITMO NEWS
With the technology, it’s possible to create copper patterns on curved surfaces, RFID tags, printed circuit boards, and microelectronic elements. The team demonstrated the process on glass, polyimide, polydimethylsiloxane, glass fiber, and even a plant leaf; they also hope to experiment with low melting point materials such as plastic.
The team’s priority task right now is to finalize their method so it may be used for industrial purposes. According to the developers, there are few similar initiatives around the world, with most being run by individual teams at research centers – however, the demand is there.
The study was supported by the Russian Science Foundation grant No. 23-73-00060.