A family of medical devices named implants are manufactured to replace a missing organ or its parts. Dental implants are implanted into the jaw to support replacement teeth. Apart from dentistry, implants are also used to resurface a knee, repair skull bones, as well as for other purposes.
All medical devices are customized to each patient's unique characteristics. In the case of dental implants, doctors must be aware of a person's skull bones, gums, and roots to determine the appropriate form and size of the future implant.
To make an implant last longer, as well as heal faster and easier, its surface is enhanced with functional features, like antibacterial properties and biocompatibility. The latter is usually accomplished by roughening up the implant's surface with sandblasting, followed by acid and anodizing to make the surface antimicrobial. So far, there is no one-stop complex to execute both procedures – except for the one currently under development at ITMO University.
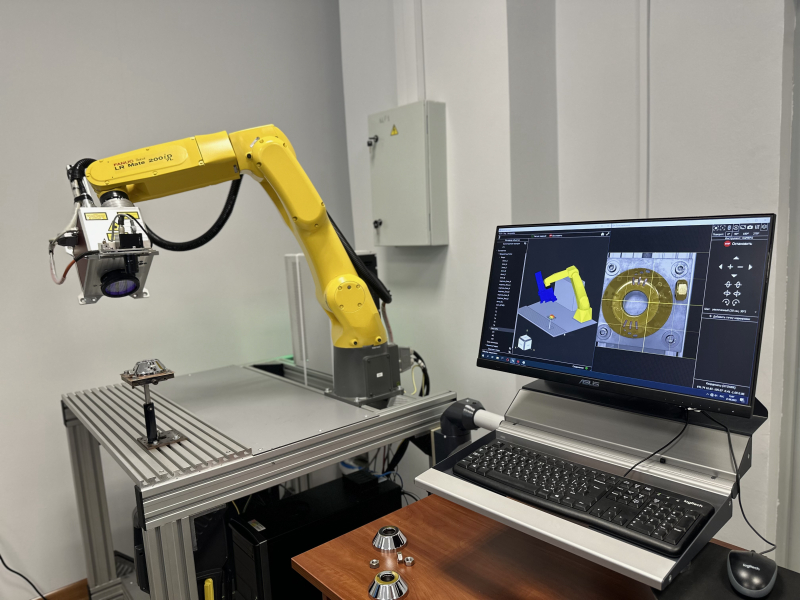
The robot laser complex. Photo courtesy of Evgeniy Shamshin
The laser-based complex
Researchers from ITMO’s Institute of Laser Technologies and their colleagues from Laser Center designed a multiuse robotic complex for surface treatment of diverse medical materials. According to the developers, the technology is equipped with a fiber laser system and possesses several advantages:
Versatility. The technology is well-suited for use with medical devices such as scalpels and surgical scissors, as well as a variety of implants, including teeth, skull, hip, and knee replacements.
Turnkey treatment in one system. The team created and merged several laser treatment options that are used consecutively:
-
The technology for antibacterial surface properties prevents bacterial complications, which lead to implant rejection. Laser heating makes oxide layers grow on the surface of a titanium implant, which demonstrates bactericidal properties when exposed to a UV source.
-
The technology for biocompatible surface property. The laser is applied to generate a relief with unique properties on the surface, followed by the laser ablation process, which creates a biomimetic micro- and nanorelief that promotes excellent adhesion of proteins in the early stages of osseointegration, cell proliferation, and differentiation, ensuring implant success.
-
The technology for applying non-toxic identification labels on medical devices. Legally binding product labeling makes it possible to track the life cycle of a product, from its early production to the end user.
“We came up with a versatile device that makes it possible to functionalize a wide spectrum of medical equipment without any additional consumables or tools. The single system can boast several treatment options, related to the biocompatible and antibacterial properties of products, their roughness, as well as labeling,” states Yulia Karlagina, a junior researcher at ITMO’s Institute of Laser Technologies.
The robot laser complex in action. Video courtesy of Evgeniy Shamshin
Compatibility with custom devices. All it takes is to load a 3D model of the implant into the program and indicate which elements of the 3D electronic geometric model need to be processed. The software was developed by the team at ITMO.
The complex consists of a six-axis robotic manipulator and a laser scanning system mounted on the robot's arm, which ensures high accuracy of laser positioning, achieved by optical methods, and universality of robotic systems. Its ability to focus a laser beam on a product’s surface in all six spatial coordinates makes it possible to process products of complex shapes in one technological cycle.
The team incorporated a computer vision system to make it easier for the operator to determine the position of the product in reality. In addition to its position, the system reports on its orientation and geometrical parameters to ensure precision laser processing.
“The existing robotic solutions are aimed at mass-production items. Once adjusted for a specific device, they perform a series of programmed actions again and again. This approach is not suitable for small-scale or one-of-a-kind equipment, whereas our technology can be easily customized for a new product,” explains Fedor Inochkin, a researcher at ITMO’s Institute of Laser Technologies.
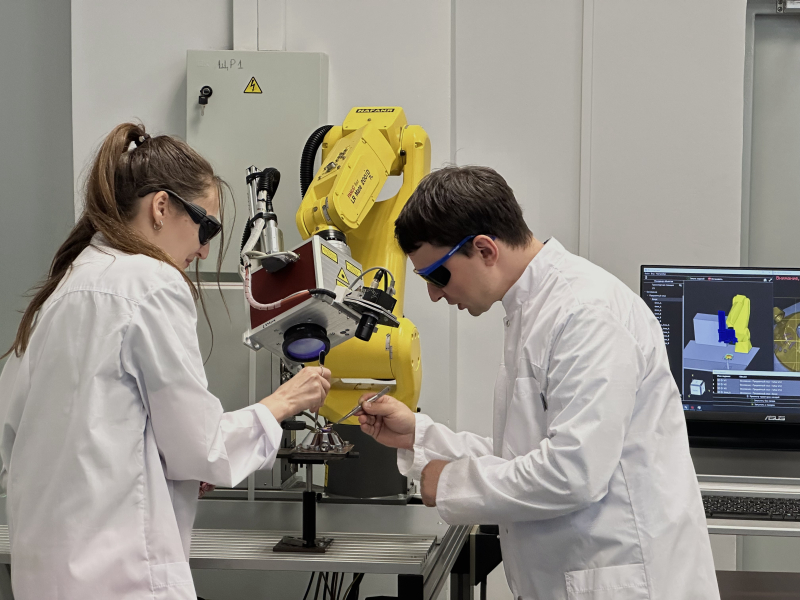
An operator positions a medical device and loads a 3D model into the system, selects the areas to be processed, and starts the program. The robot manipulator travels from one area to another with a laser beam. The procedure time varies depending on the chosen technology and item size. Photo courtesy of Evgeniy Shamshin
A compact automated laser system for dental implants and their components is another device created by the team to serve exclusively dental purposes.
“The systems have different functions, which affects their price and audience. If a customer needs to process a certain implant, like a dental one, they should purchase the second device, whereas the first one will be more beneficial with a wide range of items, including custom ones. For instance, a person who suffered from head injury can receive an individually designed skull implant. The multiuse system allows specialists to incorporate a desired set of properties into personalized implants in accordance to their unique shape,” notes Yulia Karlagina.
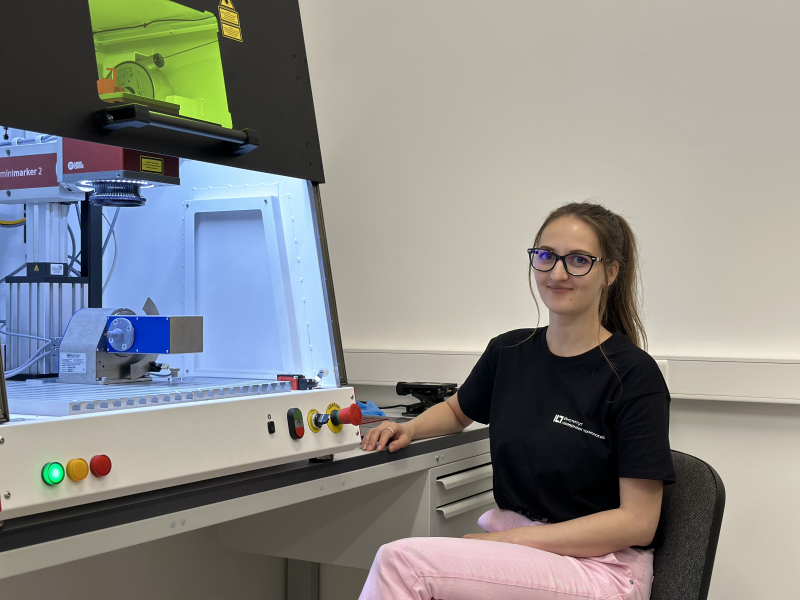
An operator positions an implant, closes the complex’s cover, chooses the type of device under study and processing mode in the program, and, finally, starts the program. The implant is ready in 10-15 minutes. Photo courtesy of Evgeniy Shamshin
Prospects of the technology
The ITMO researchers in collaboration with their co-authors from Samara State University have carried out preliminary testing of both complexes, in particular preclinical trials of the processed medical devices. All samples were successfully tested in vitro and in vivo and are recommended for clinical trials.
In the future, the developers plan to run acceptance tests to ensure the complexes are ready for operation and mass production. The team also intends to attract new industrial partners. In the long run, the systems are expected to be used in the production of medical equipment and implants.
“We already have surface functionalization technologies for implants and soon we, with our colleagues from Laser Center, will start to look for new partners who will integrate them into their productions. If requested, we can also modify our products to the client’s needs – for instance, we can add a second robot manipulator that will upload new implants into the system instead of an operator,” notes Galina Romanova, a senior researcher at ITMO’s Institute of Laser Technologies.
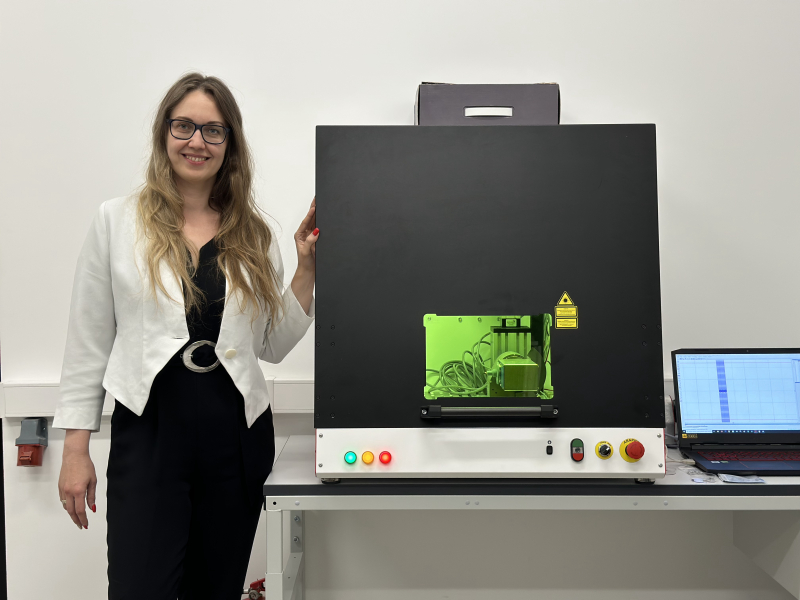
Galina Romanova. Photo courtesy of Evgeniy Shamshin
The project is implemented as part of the Government Decree No. 218 on request by Laser Center. Additionally, the developers continue to run research within ITMO’s 2030 Development Strategy.
The research team has been working on the processing of medical titanium alloys for several years now. Together with their partners from Lenmiriot, they developed a design of an implant surface that helps implants heal faster without inflammation. In 2022, Lenmiriot announced the market launch of the dental implants made with the new laser technology.