Гутное стекло и как с ним работать
Представьте, что стальной стержень — это яблоко, а печь — это банка горячей карамели. Чтобы начать создавать собственное стеклянное изделие, таким стальным стержнем — полой стальной трубой или стеклодувной трубкой — вам придется набрать расплавленное стекло из печи, нагретой как минимум до 1380 градусов Цельсия, при этом не забывая, подобно яблоку в карамели, постоянно вращать его для равномерного набора стекломассы.
После, набрав стекло, уже можно приступать к процессу. Например, если вы хотите создать сразу несколько похожих изделий, можно воспользоваться техникой ручного выдувания в формы. Но, если необходим абсолютно уникальный предмет, мастера используют технику свободного выдувания. Стеклянные изделия, выполненные по такому принципу, и называются гутным стеклом. Корни названия уходят еще в Средние века, в котором появились первые мастерские, где стекло создавалось таким способом («hutte» с немецкого и есть «стеклодувная мастерская»).
В этом случае мастер выдувает стекло через трубку в расплавленный шар, подправляя щипцами. То, что получилось, снимают с трубки и помещают на железный стержень. Уже здесь со стеклянным шаром можно сделать абсолютно все, что позволит фантазия — раскрыть верх, раскатать низ, вытянуть, согнуть или разрезать с помощью специальных инструментов.
Три в одном
Именно таким способом уникальные стеклянные предметы делают в мастерской Академии Штиглица, используя печь собственного производства. Первый прототип разработки собрал учебный мастер кафедры керамики и стекла академии Иван Козицын. В отличие от гигантских печей на заводах, которые не выключаются годами и плавят сотни килограммов стекла, его изобретение работало с гораздо меньшим количеством материала. Позже в академии задумались: а что если сделать печь еще меньше, максимально снизив затраты и позволив мастерам, которым не нужны большие тиражы, создавать штучные изделия? Так и родилась идея стартапа GUTTE.
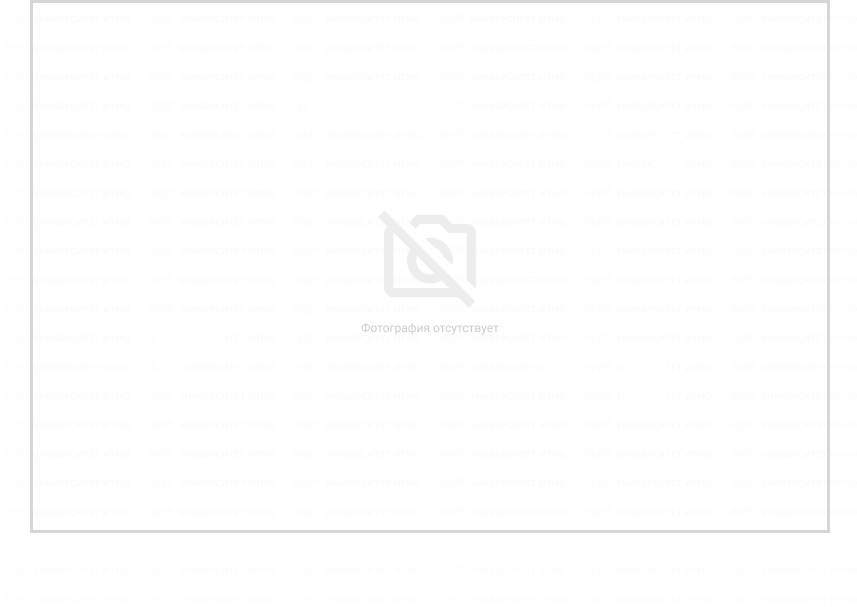
«Ситуация в целом у нас в стране развивалась следующим образом: в Советском Союзе были заводы-гиганты, которые занимались стеклом. На том же Ленинградском художественном заводе стояли гигантские печи, шло поточное производство, где сидели отдельные штаты художников, выдувальщиков. Печи работали на таких заводах безостановочно, потому что, если печь выключить, она „умрет“. Но этот процесс очень затратный. Ведь чтобы изготовить изделие, нужно расплавить огромное количество стекла, это гигантские расходы на электроэнергию, это особенные помещения и так далее», — рассказывет руководитель проекта Тамара Ковалева.
В 90-е, после того как большие заводы стали закрываться, заполнить образовавшуюся нишу было некому. Начинать с больших тиражей не будет ни один предприниматель, а работать на маленьких объемах не позволяло оборудование. Уже тогда Иван Козицын задумался над технологией, которая позволит работать с гораздо меньшим количеством материала. В 2015 году он получил патент на тигельную печь, плавившую 30 килограммов стекла. А спустя год команда академии решила пойти дальше и усовершенствовать разработку, сделав ее еще меньше и соединив в одной сразу три печи.
«Мы провели маркетинговые исследования и выяснили, что российских производителей такого рода оборудования нет, а зарубежные аналоги — преимущественно американского, немецкого, шведского производства — раза в 3−5 дороже. Кроме того, экономически они не будут выгодны потому, — продолжает Тамара Ковалева. — Для такого рода производства требуется три печи: это печь, где в тигле плавится стекло, так называемая печка-кукушка, где стекло разогревается в процессе формирования изделия, и печка для отжига — шкаф, где стекло в течение суток остывает при температуре 500 градусов. Мы же предложили такое конструктивное решение, которое позволяет соединить эти три печи в одной. Наша печь небольшая, ее можно поставить куда угодно. И в ней можно расплавить всего до 8 килограммов стекла так же качественно, как в заводских печах, которые плавят десятки килограммов материала. Она у нас в академии уже работает и показала свою эффективность«
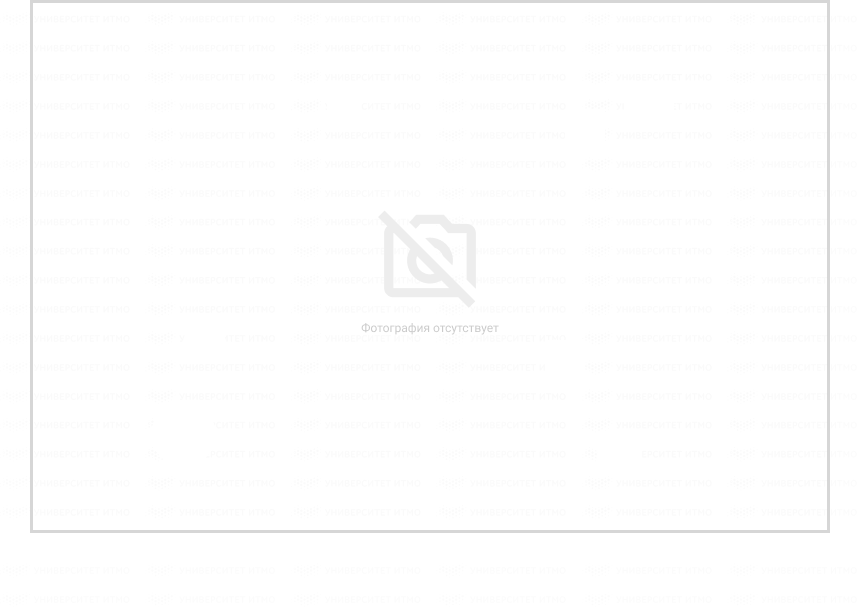
Параллельно команда проекта стала работать с Университетом ИТМО и вошла в число резидентов акселератора Future Technologies. За год работы удалось выполнить профессиональный промышленный дизайн печи, сделать ее еще меньше и функциональнее, рассказывает руководитель проекта. Здесь же стартап приобрел окончательное название, а также сформировал дальнейшую стратегию развития.
«В первую очередь мы будем работать над совершенствованием разработки с точки зрения уменьшения себестоимости, облегчения корпуса. Сейчас мы ведем на основе этого прототипа дальнейшую работу по улучшению характеристик. В дальнейшем для нас очевидно, что производство будет расти, это будет целый комплекс. Мы планируем производить печи и под свои нужды, и под нужды потребителей — небольших предприятий, которые тоже готовы выйти на рынок со своими изделиями. Плюс, я думаю, что мы будем рассматривать разные варианты, в том числе возможность аренды оборудования», — говорит руководитель проекта GUTTE.
Один секрет все-таки есть
Но если секреты стеклодувов теперь не являются тайной и для предпринимателей, которые сами смогут попробовать на минимальном количестве материала изготовить небольшой тираж собственных изделий и вывести их на рынок, то производство самого стекла все же остается уделом немногих. Команда проекта GUTTE в будущем готова освоить для себя и эту нишу. Помимо стеклодувных печей на заказ, в Академии Штиглица планируют наладить и производство собственного стекла.
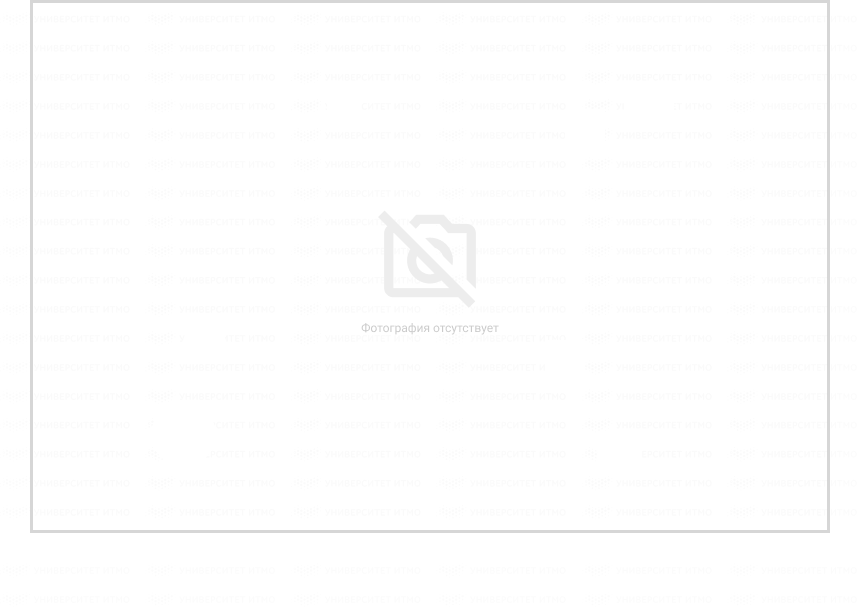
«Кроме того, что нам нужно увеличить линейку печей, нам необходимо разработать и запустить производство сырьевого материала, то есть непосредственно художественного стекла, чтобы таким образом обеспечивать полный цикл производства. Сейчас все стекло американского производства, и после 2014 года оно, конечно, стало очень дорогим. Поэтому мы видим здесь свободную нишу для нас. В ближайшей перспективе мы планируем построить лабораторную печь, не отрываясь от учебного процесса. В ней будут делаться непосредственно пробные замесы варки стекла. Разумеется, здесь будет секрет производства, потому что состав стекла всегда уникален», — уточняет Тамара Ковалева.
Устойчивые образцы стекла собственного производства команда проекта GUTTE намерена получить уже через три месяца. Подробнее о проекте вы сможете узнать на DemoDay акселератора Future Technologies, который пройдет уже сегодня, 18 февраля. Здесь же можно будет увидеть, как создаются изделия из гутного стекла, и даже попробовать сделать их самостоятельно.