How long have you been working on the project?
It was a practice-oriented R&D project that engaged Bachelor’s and Master’s students in robotics for a little over a year. In April 2020, we launched the development and this June the team completed the robot’s testing.
What are the unique design features of the manipulator?
Our solution is different from other manipulator robots because we employed polymers as our primary construction material, while the majority of parts were made with a 3D printer or the laser beam cutting technology. Robots with metallic parts are expensive and are only cost-effective in mass production. This is one of the reasons why there aren’t many robot manufacturers in Russia. It’s easier to buy something ready-made because small-batch or individual production makes robots even more expensive. We created a robot that is relatively cheap to manufacture but at the same time secure and able to exactly reproduce its movements or position itself.
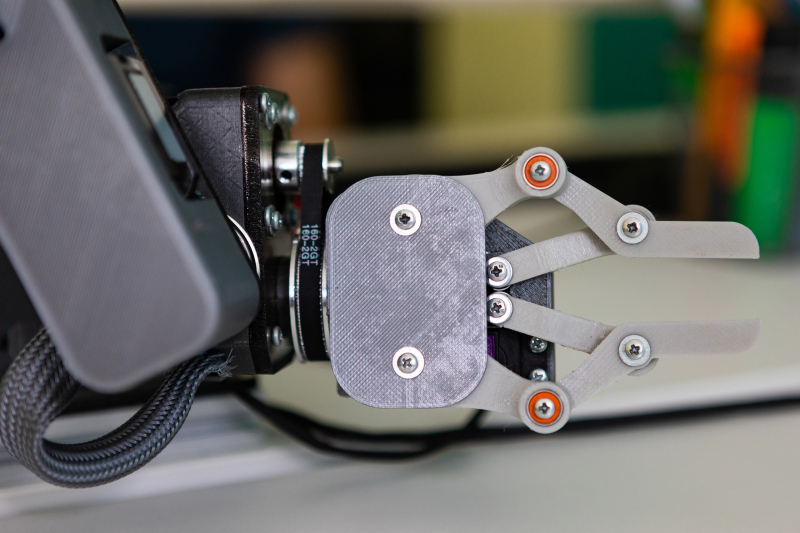
Manipulator arm. Photo by Dmitry Grigoriev, ITMO.NEWS
How expensive is this new manipulator arm compared to its analogs?
Those six-axis robotic arms available on the market cost over a million rubles (about $13,605), while we are planning that our product will cost under 300,000 rubles (about $4,000) upon commercialization. And if we start mass production, the price will get even lower.
There is another compact manipulator arm on the international market, but it's made mainly from aluminum – and thus costs as much as a large-scale industrial manipulator.
Moreover, as 3D printers are gaining popularity, there are many enthusiasts trying to develop robots with printed parts. Usually, though, they don’t take many important features into account, which makes such robots’ movements not very precise and thus unreliable. We’ve analyzed all such solutions at the start of our project to identify the most common mistakes.
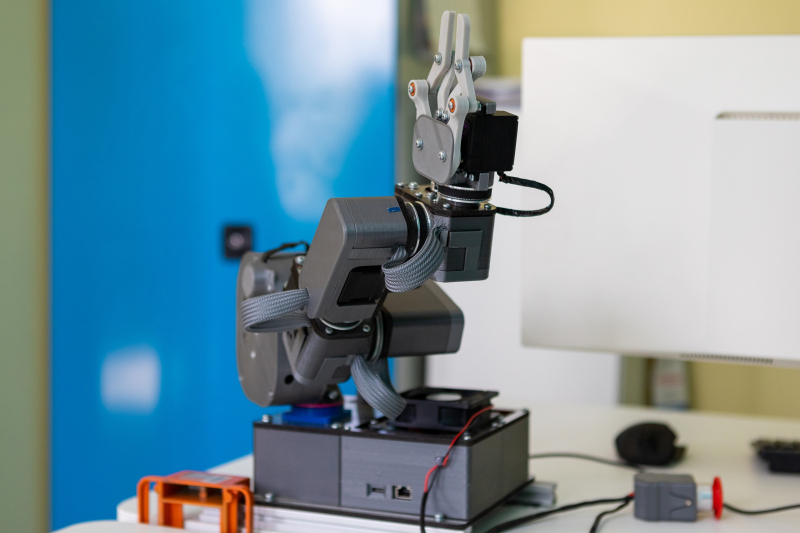
Manipulator arm. Photo by Dmitry Grigoriev, ITMO.NEWS
Which parts were made with a 3D printer?
Many of them but we can’t say that separate segments were completely 3D printed. It would’ve been unwise to make drive and actuator shafts from polymers. Each link of the manipulator has about 80% of 3D printed parts, mostly those with complex shapes.
We combined different types of polymers: simple shapes were made from hard and solid polymer sheets, while complex shapes were 3D printed. This combination allowed us to create parts that are cheap to produce and yet demonstrate all the necessary properties. We thought about aesthetics, too, so we put most of the robot’s wires inside. What we have is still a prototype but it is ready for any challenge.
What are the tasks that the new manipulator was made for?
It’s a multipurpose robot that resembles a human arm. It’s capable of a wide range of tasks limited only by its workspace and the type of gripper used. Our prototype has a mechanical gripper which allows it to capture solid objects, but it can be equipped with a vacuum one – it’s widely used in the industry thanks to its multifunctionality and simplicity. The robot’s main task is to change its position or interact with the objects around it, and the purpose of such interaction is all up to the operator.
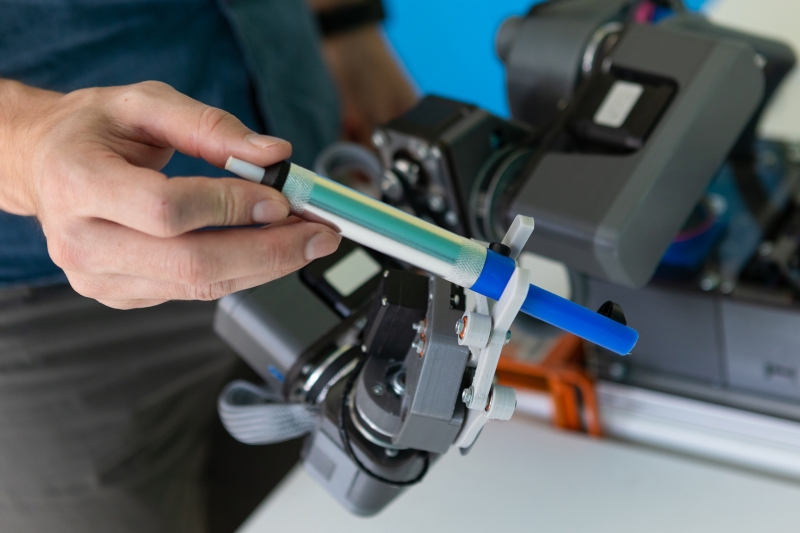
Photo by Dmitry Grigoriev, ITMO.NEWS
What are the fields where the robot can find its potential applications?
We aimed to cut down the price to serve the fields where automation with the robots present on the market is now unprofitable. For instance, the service industry. Take foodservice, for example, where there are many routine operations that could be automated. Especially given the repetitive tasks in fast food restaurants or cafes – they are simply calling to be automated. But these days it’s cheaper to hire an employee for the job. If robots get cheaper, it will give us the chance to automate routine processes.
Another potential application is packing several goods into one box. The six degrees of freedom allow the robot to capture objects in various orientations and place them in the needed locations the correct side up. Our manipulator arm can also be used at a chemical laboratory by only changing the gripper so that it can capture tubes and other tools.
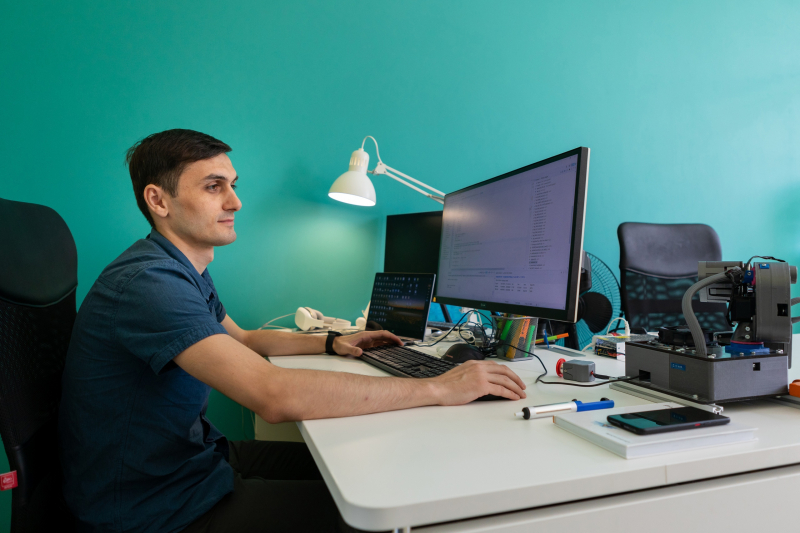
The process of controling the new manipulator arm. Photo by Dmitry Grigoriev, ITMO.NEWS
How is the robot controlled?
The robot connects to a computer to download an algorithm, a set of operations performed by its drives. Using the software we developed within the project, users can also update the algorithms with no programming skills needed. By using buttons to control the robotic arm movements and saving the key points it has to pass, users can automatically generate a new algorithm. The system will also check for any errors in the algorithm. If the new set of operations performs the task well, it can be set to repeat in the same window of the user interface.
How are you planning to develop this project?
Now we only have a prototype with the bulk of functions to test the robot’s mechanics. Because of the new materials used, we had to change our approach to design. We focused on mechanics first with the control system serving as a necessary component to make the mechanics do what is needed. We are planning to polish the control system and then, later, enter the market. But first we have to test the various modes that the robot can be used in. We haven’t yet conducted any large-scale tests, we haven’t even left the robot on for 24 hours – so those are our plans for the nearest future. Then, we intend to commercialize our project.