Making factories smart
Even though industrial automation is a global trend, not every business has successfully incorporated digital solutions into their workflow. Oftentimes, factory operators still have to deal with a lot of paperwork, which makes it impossible to keep track of production in real time – or quickly deal with arising problems. Some of them are increasing equipment productivity, installing new machines, or optimizing production pipelines to avoid defects. All of these decisions affect a company’s income.
Manufacturers all over the world believe that these questions can be handled by smart factories that are part of the so-called fourth industrial revolution. What makes them smart?
It’s true that automated processes and industrial robots are no novelty – they have been used for decades in some industries. These technologies include barcode scanners, cameras, and digital equipment. However, they are typically not interconnected – and that’s what makes smart factories so different: they integrate machines, people, and big data into a single digital ecosystem, eventually making a digital twin of the production process.
Here’s a practical example: a human machine operator receives a digital description of their task; they then choose the right materials and tools for it and set up the machine’s parameters; after a while, they receive the completed product. If the task has been completed, the system receives one signal and if there are any problems – another. This way, the staff can quickly spot and address the problem, which is especially beneficial for productions involving hundreds of machines.
Moreover, smart factories create IDs for each final product with information on the ideal manufacturing conditions. This data can be analyzed by an AI to increase production efficiency and quality.
“Any production would benefit from a digital twin, but they would come especially handy for factories with numerical control equipment or productions where the cost of technology violations or wait is high. Among such productions are aircraft and machine engineering, shipbuilding, laser, and optics industries,” shared Mikhail Ponomarenko, a PhD student at ITMO’s Faculty of Control Systems and Robotics, the head of production solutions at ASCON.
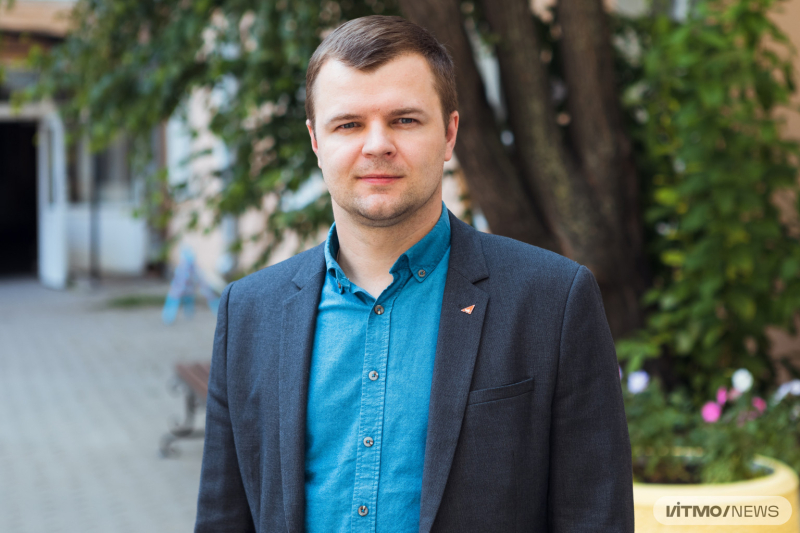
Mikhail Ponomarenko. Photo by Dmitry Grigoryev / ITMO.NEWS
Needless to say, it is not an easy task to introduce a unified information system in production, not least because there isn’t a single one-fits-all automation method. That’s why it is often accomplished in stages: first, smart factory software is offered to engineers; later, it is expanded to involve the production.
There are several reasons behind this approach. First of all, some of a factory’s machines might be too old to connect to new software, while it isn’t always possible to install updated equipment. Second, the new equipment’s software might also not fit into the unified information system. Finally, the industry needs more specialized experts – which calls for the creation of new learning materials on automation and digitization.
A solution by ITMO and ASCON
In collaboration, experts from ITMO and ASCON have developed an automation method and a smart factory based on an active experimental production that was created in December 2022 at ITMO’s Engineering and Technology Center. There, students conduct their research projects and complete assignments for partner companies, such as parts for optical systems, various devices, and sensors.
Using the COMPAS 3D software suite provided by ASCON, ITMO students have made a digital version of the space and equipment of the experimental production, complete with units for mechanical processing, general equipment, and control and measuring machines, as well as a 3D printer, a coworking space, and lecture rooms. Moreover, the team has programmed a controller that imitates production machine management.
This September, ITMO is planning to purchase additional equipment, while ASCON will provide digital solutions for an automated factory management system. For instance, students will be able to use a computer-aided manufacturing system to write programs for factory machinery. Once those are complete, they will be delivered to each individual operator via the Golfstream management system. The WINNUM equipment monitoring system will provide insight into the state of each machine – whether it’s inactive, runs at full, or partial capacity. This information will be available as part of the production’s digital twin.
Eventually, the experimental production will be completely automated, while ASCON’s products will make it possible to visualize the entire production process, from the first design to the final product, as well as analyze the results and plan future assignments.
Acquire real-life applied skills at ITMO
The developed mockup and software will be available to students of ITMO’s Master’s programs Digital Control Systems and Digital Technologies in Manufacturing. These solutions, combined with special learning materials developed by ASCON, will allow students to learn their way around a modern production, as well as gain practical experience of completing production tasks.
“With our mockup, it’s possible to model various production situations in laboratory conditions. This allows students to try their hand at solving a wide array of tasks, such as planning equipment load, designing production logistics, programming controllers, and using predictive analytics to prevent any accidents,” commented Yury Andreev, an associate professor at the Faculty of Control Systems and Robotics.
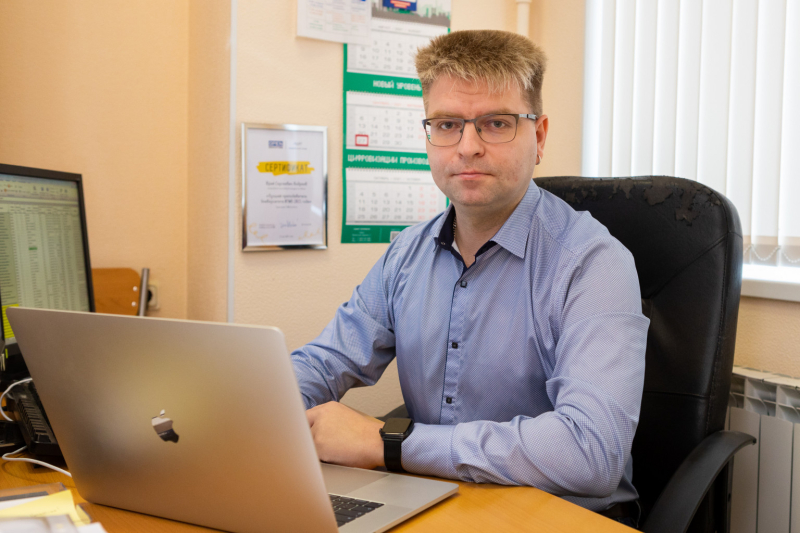
Yury Andreev. Photo by Dmitry Grigoryev / ITMO.NEWS
Dr. Andreev also added that the mockup was created in the unified information environment, making it compatible with big data processing tools that can be used for production optimization. Next, the team from ITMO is planning to progress from a digital mockup to a digital factory.
Apart from working with the mockup, students of the two Master’s programs will learn to use cutting edge digital tools to increase production efficiency. At the program Digital Control Systems, students will develop control algorithms and design sensors to be used in automation systems, while the program Digital Technologies in Manufacturing will offer training in automation tools, 3D modeling and engineering analysis systems, as well as industrial robot programming. Graduates will be able to use this knowledge to develop smart factories and digital productions.
Also within these programs, students will be able to intern or land jobs at Systeme Electric, Diakont, Etalon, and others. For instance, Mikhail Ponomarenko got a job as manager at ASCON as a Master’s student, and now he combines his PhD studies with his responsibilities as the head of production solutions at the company.
Admissions to Master’s programs Digital Control Systems and Digital Technologies in Manufacturing are open on ITMO’s Admissions website until August 4.