Процесс разработки
На интеграцию имплантата в костную ткань влияют два фактора: хирургия (опыт врача, стерильность, дальнейшее медицинское сопровождение) и физическая составляющая (размер, форма и рельеф поверхности имплантата). Лазерная обработка титана позволяет бесконтактно воздействовать на поверхность изделия и менять ее рельеф на микро- и наноуровне. Технология исключает необходимость использования кислот или абразивных частиц, которые остаются на поверхности и являются одной из причин короткого срока службы имплантатов — до 10–15 лет.
Во время исследований ученые смотрели, какой рельеф лучше всего подходит для биосовместимости инородного тела с костной тканью: это должны быть лунки, протяженные канавки или неупорядоченная структура. Протестировав на клетках несколько вариантов, ученые ИТМО нашли наилучший: протяженная структура в виде микроканавок, размер которых соизмерим с клеточным. За счет этого можно управлять направлением роста ткани. Полученная технология была использована для производства дентальных имплантатов.
Использование в производстве
Ученые ИТМО совместно с крупнейшим в России стоматологическим фрезерным центром полного цикла производства и заводом Lenmiriot, входящим в группу компаний «ОРТОС», а также Санкт-Петербургским государственным медицинским университетом им. И. П. Павлова использовали разработанную технологию для производства дентальных имплантатов. По словам разработчиков, аналогов подобного применения метода в коммерческих целях в России и мире единицы.
«У каждого человека своя структура кости, поэтому под каждый случай требуется свой вид имплантата. Завод Lenmiriot изготавливает более 100 видов, которые имеют разные размеры, форму, конусность. Для всех их нами была создана технология обработки», — рассказывает Юлия Карлагина, исполнитель проекта, сотрудница Международной научной лаборатории лазерных микро- и нанотехнологий и систем ИТМО.
Процесс создания имплантата с заданными свойствами поверхности
Процесс производства каждого имплантата многоступенчатый и полностью осуществляется на заводе Lenmiriot. Берется титановый пруток, из которого с помощью микрофрезерования по 3D-модели вытачивают будущий имплантат необходимых размеров. После он проходит несколько этапов очистки и лазерную обработку, которая занимает от 20–40 минут в зависимости от формы и размера изделия.
Будущее технологии
Цель следующего проекта — создание идеального имплантата, имеющего три функциональные зоны. Первая — корень с микроканавчатым рельефом, который обеспечивает сращивание с костной тканью. Вторая — шейка с биомиметическим рельефом и антибактериальным покрытием для закрепления изделия и предотвращения формирования бактериальной биопленки. Следующая — абатмент (элемент протезирования, соединяющий коронку с имплантатом) с гладкой поверхностью, имеющей различные цвета (голубой, желтый и другие), это получается также за счет лазерной обработки. Он обладает антибактериальными свойствами и выполняет функцию индикатора для стоматологов.
«Мы также работаем над созданием способов обработки поверхности других видов имплантатов и приданием им различных функциональных свойств. Кроме того, сейчас идет разработка полностью автоматизированной технологии создания индивидуальных титановых мембран с антибактериальными свойствами, которые будут созданы с применением искусственного интеллекта и нейросетей», — комментирует Юлия Карлагина.
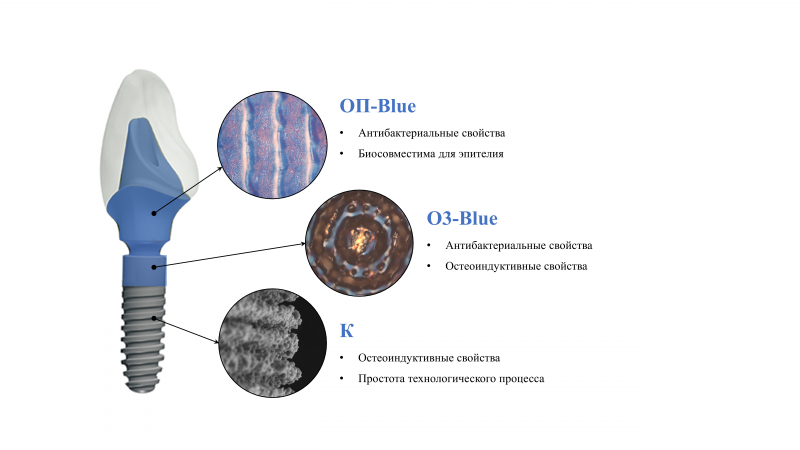
Концепция имплантата. Изображение предоставлено сотрудниками лаборатории лазерных микро- и нанотехнологий ИТМО